Environment
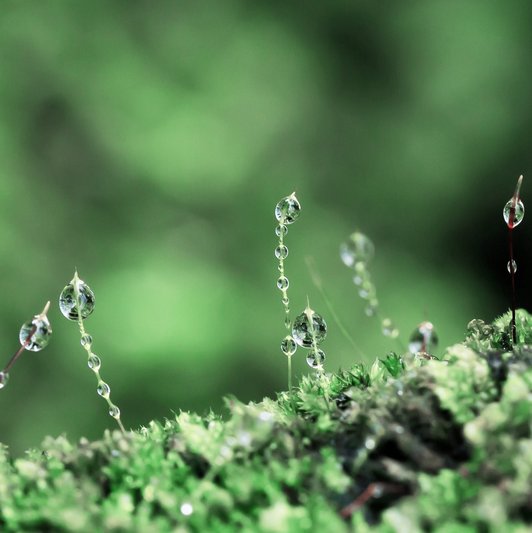
Climate change
In a world where the impact of our actions is increasingly affecting the environment and our society, it is more important than ever that companies and organisations take their responsibility for a sustainable future seriously. As a specialty chemicals company, we are aware of the impact of our production activities on the environment. By handling resources responsibly together with reducing emissions, as well as by a circular economy and, not least, a sustainable product portfolio, it is up to us to minimise the negative effects on the environment. In our climate roadmap, we have set ourselves ambitious goals and are taking a variety of measures to be climate neutral by 2033.
To achieve these goals, the Alzchem Group has installed a comprehensive, integrated management system (IMS) for environment, safety, health, quality and energy management, based on legal framework requirements as well as internal guidelines, procedural instructions, responsibilities and tasks.
We regularly monitor, document and evaluate the impact of our activities on the environment by identifying environmental key figures, thereby supporting the targeted improvement of our environmental performance. By presenting environmental performance in the context of sustainability key figures, a quantitative overview of the most important trends for Alzchem is provided. The use of flue gas (CO2 ) in the production process enables us to reduce the amount of CO2 emitted annually by 50,000 tonnes. With the CO2 quantities used in the production process and the increased amount of energy from heat recovery over the past three years, we have been able to make a positive contribution to climate protection. Our NOX emissions have dropped significantly in recent years due to various improvements in fuel quality. Furthermore, we have been able to keep our overall dust emissions at a very low level.
To evaluate our environmental performance, we use the requirements of EMAS and the internationally recognised standard for environmental management ISO 14001 as a basis. We check the implementation of the certifications of our production sites with numerous internal audits as well as annual monitoring audits by an external monitoring company as part of the re-certification or re-validation process. The individual companies of the Alzchem Group also carry out supplier and customer audits, in which environmental aspects are considered in addition to quality issues.
Compliance with the requirements of both licensing notices and environmental law for the operation of our plants is regularly checked by the responsible authorities. In order to be able to carry out these checks as efficiently as possible for both the monitoring authority and the Alzchem Group, a special project was set up in cooperation with the authorities and other companies in the "ChemDelta Bavaria" (joint initiative of the companies in the Bavarian chemical triangle), the so-called "cooperative plant monitoring" model.
Alzchem's climate roadmap
In order to continuously reduce emissions from production processes, our experts are constantly working to further improve and optimise the processes and set-up of our plants.
The Alzchem Group invests around 24 million euros* annually in measures to improve climate protection. In recent years, it has succeeded in reducing CO2 emissions by 50,000 tonnes.
The Alzchem Group is setting a new green milestone with the ambitious goal of being climate-neutral by 2033.
With our comprehensive climate roadmap, which the Board of Management developed together with an internal sustainability committee and which includes concrete packages of measures, we want to achieve the targeted climate neutrality primarily in two ways, on the one hand through independence from fossil fuels (defossilisation) and on the other hand through climate-neutral production. Our goal is to reduce direct CO2 emissions (Scope 1) released at all Alzchem sites by 75 percent by the year 2030. We want to achieve complete climate neutrality in 2033.
Our climate roadmap towards "Net Zero" is guided by the following four principles:
- We want to close our production cycles more efficiently,
- reduce the amount of energy needed,
- make more intensive use of the waste heat generated in our production processes and
- avoid any form of waste of resources.
With the Climate Roadmap, we have developed a powerful set of instruments that will have a proud record in the end: The packages of measures described above should lead to a CO2 reduction of around 90,000 tonnes by 2030. That is more than 75 percent of our current CO2 emissions. By way of comparison: a beech tree has to grow for a full 80 years in order to absorb a single tonne of CO2.
If we consistently implement our climate plan, we will have already offset the remaining 25 percent of our emissions in 2033 and thus achieved the targeted climate neutrality. We can make this bold statement because we already know very precisely our remaining emissions in 2030. Here, we will use the latest technologies, especially in our plants.
We are already working on initial ideas and approaches to solutions. For example, replacing the steam drying process we currently use with a modern induction process promises considerable savings potential. But it is also clear that a chemical company like ours can probably not completely avoid its CO2 emissions according to the current state of knowledge. We will therefore reduce the unavoidable remaining emissions to "net zero" through appropriate compensation measures.
In our efforts to produce in the most environmentally friendly way possible, profitability is not neglected, because our investments - totalling more than 30 million euros - pay off: due to the associated measures alone, we will probably realise annual savings of around 6 million euros from the year 2030 onwards, from which we will benefit permanently. Our investments therefore make twofold sense: we not only save CO2 for the environment, but also sustainably save energy for our own processes - and thus also costs incurred so far.
With the ambitious goals in our climate roadmap, we will continue to consistently pursue the sustainability measures we have already initiated and successfully implemented in recent years. Every Alzchem employee is already making an important contribution in his or her area.
Emissions reduction along the NCN value chain
Our exhaust gas incinerators (AGV) at the Trostberg site not only clean the process exhaust air and thus lead to a continuous reduction of emissions by lowering the limit values according to the BREF approach (Best Available Techniques Reference), but also generate process heat for the manufacture of our products.
With the annual emission report of the exhaust gas incineration plant (AGV) for Trostberg Chemical Park, we inform the public about the proper operation of the AGV. As in previous years, the prescribed limit values were continuously monitored in 2022. The daily mean values were not exceeded. By operating the AGV, Alzchem ensures the reliable disposal of waste gases and chemical waters at the Trostberg Chemical Park and thus avoids unnecessary transports of hazardous waste.
In 2021, a regenerative thermal oxidiser (RTO) was also commissioned in our calcium cyanamide production at the Trostberg site.
Detailed energy management
As an energy-intensive company, we naturally pay attention to the efficient use of energy.
As part of our detailed energy management system, we carry out a systematic, energy-related assessment of all operational areas, energy performance indicators, energy targets and action plans to continuously improve energy-related performance. This increases our energy efficiency and at the same time helps us to further optimise the careful use of resources.
Use water from own sources more efficiently
Water, a vital resource for humans, is becoming increasingly scarce due to rising consumption worldwide. For us, sustainable water management has been a central component of our corporate planning for many years and an important contribution to our corporate environmental protection. This also includes adapting our use of water to the increasingly strict legal regulations. The sufficient availability of water as a resource for cooling and service water, but also as a production medium, plays a decisive role in many operational processes.
The soil conditions at our Trostberg, Hart, Schalchen and Waldkraiburg sites are characterised by thick, very porous gravel layers that contain large groundwater deposits. This geological peculiarity allows us to extract all the cooling, service and drinking water we need from our own groundwater wells. In doing so, we want to avoid damaging protected areas, sensitive ecosystems and habitats. Our goal is to continue to reduce water consumption in the future and minimise the impact on the water situation around our sites.
Our sustainable water management enables us to monitor wastewater, which consists mainly of cooling water and rainwater. Only a small fraction of the wastewater (approx. 0.5 %) has to be treated in a wastewater treatment plant.
Nordic Carbide AB's cooling water supply is ensured by the local site operator at the mouth of the Ljungan River with an average water flow of 200 m3 /s. A maximum of 0.5 m3 /s is required for carbide production, so the impact on the environment can be described as very low.
Optimisation of waste management
Avoiding and reducing waste as an environmental goal is important to us in order to minimise the negative impact on people and the environment.
Primarily, our aim is to avoid or to minimise waste from our production facilities by constantly optimising our production processes and expanding our integrated system and, if possible, to recycle it. Only if this possibility does not exist is the focus on energy recovery and only at the end on safe disposal.
As part of our systematic waste management, we use the advantages of our back-integrated NCN network system and the spatial proximity of our production sites. Through the intelligent integration of our production facilities and our production technologies, including energy and material flows, even by-products (e.g. CO2 ) can be used as raw materials with the goal of zero waste.
By-products from the production process are used by us in sometimes very different fields of application (e.g. black lime for agriculture and the cement industry). By constantly improving our production processes, e.g. through the use of special catalyst systems, side reactions can be minimised.
In recent years, we have succeeded in significantly reducing the amount of waste at our sites, e.g. by recycling used containers. The remaining, unavoidable waste is recycled externally.