Practical experience Eminex®
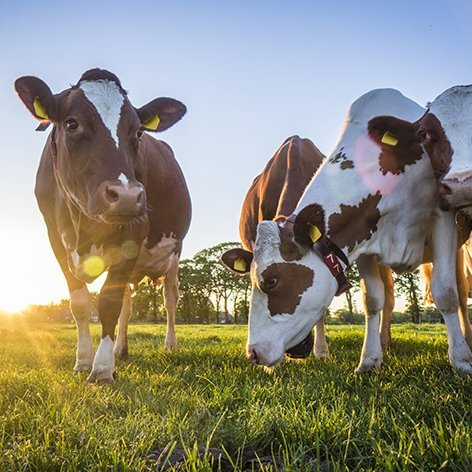
Martin Rietmann-Regelink’s farm
Puts a stop to foaming slurry
This is how the family-run farm in Neuschow in East Frisia described the advantages of Eminex® slurry additive.
“Homogeneous slurry, suppression of foam formation and no methane emissions,” explained Martin Rietmann-Regelink, summing up the advantages of Eminex®. He runs a dairy cow farm with a herd of 150 dairy cows, plus their calves, with his wife and their daughters Esmee and Maureen.
Recommendations from practice
On the Rietmann-Regelink’s farm, the significant foam formation on the slurry meant that a lot of the barn’s storage capacity was lost. In some areas, the foam layer was 50 to 60 centimetres thick and sometimes even overflowed onto the slatted floor when conditions were not favourable. Esmee was actually the one that came up with the solution for the farm’s slurry problem. They were having a similar problem with foaming on her training farm. “Since we started using the slurry additive Eminex® on my training farm, foaming slurry has been a thing of the past. So I thought it would be worth a try on our farm too!” explained Esmee.
Goodbye to foaming slurry
“At the start of October, we added 1,200 kilograms of Eminex® to 600 m3 of slurry. Since then we have had no more foam formation and the slurry is much more homogeneous,” explained Martin Rietmann-Regelink happily. “When we spread the slurry it flowed much easier and more could fit into the tank due to the lack of foam!” Even Esmee and Maureen, who want to take over their parents farm in the future, were convinced by the product. “The advantages in the barn were clear. No foam, homogeneous slurry and much better air in the barn,” explained Esmee. “We wanted to make our milk production as carbon-neutral as possible in the future. This is why we decided to use Eminex®,” added Maureen. The slurry additive won the whole family over. “I only wish that the significant reduction of methane emissions from slurry thanks to Eminex® was recognised and promoted more,” concluded Martin Rietmann-Regelink.
Ingo Harms’ farm
No foam formation
Ingo Harms runs a dairy farm comprising 140 dairy cows, a loose cubicle housing system and 101 hectares of farmland in the East Frisian village of Ihlow, Germany.
“A layer of foam 50 to 60 centimetres thick ran over the slats in some places. This took up a lot of storage space for us. The fermentation odour coming from the foam also caused the cows’ eating performance to drop. Once it reached a certain capacity, the slurry pit could no longer be stirred, which meant we had to spread the slurry without being able to stir it up first. As a consequence, a higher proportion of thick slurry
remained in the slurry pit”, explains Harms.
While searching for an additive that would homogenise the slurry and prevent foam formation, he happened to come across Eminex® in late 2021. When he first applied the product in early 2022, he stirred in two kilograms per cubic metre of slurry. “We simply lifted a big bag over the slats with a loader”, says Harms. The additive that had been tipped onto the slats was then added to the slurry using a big bag dispenser.
At this point, the pit was half full. Eight weeks after he applied the product, Ingo Harms is still very happy with the results – homogenized slurry with no foam or crusting. “Despite the pit being quite full, the slurry is still much more consistent and visibly fluid! The cows also maintained their performance over winter. I put that down to the lack of foam this year too. We didn’t expect to see such clear results”, explains Harms excitedly, and adds, “we want to use Eminex® for our young stock in future too. The slurry in this area of the farm is especially thick due to the amount of straw we use. We spread the slurry onto our 70 hectares of permanent grassland using a drag hose or trailing shoe applicator, so I’m hoping the improved consistency will make it easier to spread. The runnier and more consistent the slurry, the better it penetrates the soil and the better the nutrient utilisation. This is hugely important for our farm given its location in a water protection area. It also has the significant side effect of preserving nitrogen in the farm‘s circular economy and increasing the value of the slurry”, summarises happy customer Ingo Harms.
Dirk Janssen’s farm
“I‘d like the milk we produce to be carbon-neutral in future”, proclaims 30-year-old Dirk Janssen, who runs a dairy farm of 220 cattle alongside ten neighbouring holiday homes in the village of Neuharlingersiel, Lower Saxony, Germany.
“With our farm’s public image in mind, I was looking for a product that could reduce the emissions coming from our slurry. In early November last year, I came across Eminex®, which we applied at a ratio of one kilo per cubic metre of slurry to great effect”, explains the graduate farmer. There was no foam on the slurry, nor any crusting.
“In order to convince ourselves and, above all, our holiday guests of the effectiveness of the product, we started a comparative test of treated and untreated slurry in parallel.” The test involved filling two containers with 10 kilos of slurry each, one treated and the other untreated, then hermetically sealing them and connecting them to a gas projector. After two weeks of storage, methane was visibly accumulating in the gas projector of the untreated slurry, whereas no evidence of gas formation was found in the gas projector connected to the Eminex®-treated slurry.
“Now, a few weeks later, the gas projector of the untreated slurry is at bursting point, while the Eminex® in the treated slurry container continues to have a lasting effect”, reports Janssen. But it‘s not only the methane reduction that the farmer and the holiday guests he‘s talked to so far appreciate. “Something else I find brilliant with Eminex® is that it minimises odours in the cattle shed. That goes down really well with our holiday guests”, says the farm manager enthusiastically.
Gerrit Eberhards‘ farm
Comparative effect of Eminex®
Along with his family, Gerrit Eberhards runs a dairy farm in Friedeburg, Lower Saxony in Germany that had a new loose cubicle shed for 160 dairy cows installed two years ago.
When he first applied Eminex® in autumn 2021, his expectations were clearly defined: the slurry was to be more fluid, its methane emissions reduced, and less foam was to form on the slurry. “In order to directly compare the effects of Eminex®, we only used the product in one slurry pit”, explains Eberhards, who was not completely convinced of the product‘s effectiveness before he applied it.
At the start of the ‘product test’, there were around 600 cubic metres of slurry in the pit. One kilo of Eminex® per cubic metre was added to the slurry via the big bag dispenser and mixed in using the slurry mixer situated in front of the cubicle building. The farmer was not disappointed with the results. In fact, he was impressed: “The initial differences were visible as early as December. There was much less foam formation in the Eminex® pit. This pit didn‘t have any crust formation either. When compared directly with the other pit, that was a major difference. To maintain this effect now that the amount of slurry has increased to 1,200 cubic metres, we added again Eminex® in early 2022”, says Eberhards
According to his estimations, the product definitely represents value for money: “We have nine slurry pits in total on our farm, so crust removal is a very labour-intensive activity. Eminex® enables me to save valuable time stirring the slurry, which of course saves money too”, says the farmer, adding, “we spread our slurry directly onto the ground, so I’m hoping that with the knowledge we‘ve gained about the effectiveness of the additive, we’ll be able to improve our slurry spreading operations even further due to the enhanced fluidity of the slurry. I also hope that the slurry itself will be more effective due to the more consistent nutrient distribution and a combination of mineral and organically bound nitrogen.” Eberhards plans to spread the slurry he‘s treated with Eminex® right alongside the untreated slurry in order to identify any potential differences in the ‘enhanced’ slurry. The farmer‘s verdict is already certain, however: “Eminex® has impressed us so much that we have decided to use it in our other slurry pits in future too.”
Christian Braun’s farm
“No foaming, homogeneous slurry and an improved housing environment” – the benefits of Eminex® have won over Christian Braun from Riedlingen-Neufra.
Christian Braun farms around 180 hectares, 50 of which are grassland, and operates a bull fattening barn with enough space to house 280 animals.
With his fleet, which consists of three combines and three maize choppers as well as several other vehicles, he also works as an agricultural contractor for other farms in the region. Due to the major problems he faced with slurry foaming last year, the farm manager decided to use the slurry processing additive Eminex® in his barn. As the rearing barn has two identical cellar systems, the effects of the slurry additive could be compared with the untreated slurry. In mid-November, 1.2 kilograms of Eminex per cubic metre of slurry was stirred in and in mid-January another kilogram of Eminex per cubic metre of slurry was added. Braun and his team built a doser to evenly distribute the additive into the stirred slurry over a period of around three hours. “The results were very convincing,” explained Braun proudly. “In the cellar treated with Eminex there was no foam formation, the floating layer was significantly thinner and the slurry was easier to stir than in the untreated cellar. We were also able to ensure a better living environment for our cattle in this part of the barn.” At the end of March, both slurry cellars were stirred ready for spreading with the spreader and Braun’s initial impression was confirmed. The treated slurry was more homogeneous and free from foam, whereas the untreated slurry had a significant foam formation with a layer over 70 centimetres thick. Despite the heavy rain, the untreated slurry had to be moved “because the bulls were standing in foam,” explained Braun. “The treated slurry was equally homogeneous from the first to the last tanker,” confirmed his colleague. After this experience, Braun was won over by the effects of Eminex® . “Even now there is still less foam in the treated cellar than in the untreated cellar,” he reported. “In any case, this winter I’ll be treating both cellars.”
Georg Pupkes‘ farm
Homogeneous and flowing slurry
In Ihlow in East Frisia, Georg Pupkes and his family run a farm with 230 dairy cows and 150 hectares of agricultural land.
Gases result in foam formation
For years he had been having problems with his slurry storage. In spring the slurry cellars formed a thick floating layer on top which made stirring the slurry very difficult. He often had to add water before spreading and even then the slurry had to be stirred for up to four hours before it was ready to be pumped.
Plenty of storage space thanks to Eminex®
During the farmer’s search for a solution to the problems with the floating layer, one of his neighbours recommended Eminex®. According to the neighbour, the granular form of the slurry additive really helped him to tackle foaming and the formation of floating layers on his farm. So in December 2022, 40-year-old Pupkes tested out Eminex® for the very first time in both of his 800 cubic metre slurry cellars. He added two kilograms of Eminex® per/m³ of cow slurry available. "It's very easy to use. Using a wheeled loader, we lifted a big-bag over the slatted floor and added the additive to the slurry with a dosing slide,” explained Pupkes, who was very happy with his experience. “At the start of March, we had to empty both cellars. The slurry treated with Eminex® was significantly more homogeneous and flowed better, in fact the cellar was pumped empty in just 20 minutes. With the untreated slurry, we first had to add water and then we had to mix it for one hour.”
What’s more, as the floating layer had been dissolved there were no blockages in the hose during the spreading. This was particularly important to the farmer, as he needed to spread the slurry on 50 hectares of his permanent grassland with hoses and trailing shoes. Overall, during the test he was able to save a lot of money when it came to the addition of water and the stirring. In addition, Pupkes estimated that by having a more homogeneous and flowing slurry, the nutrient distribution and supply of the soil was improved. “I plan on using Eminex® in both of my slurry cellars in the future. I hope that it’s equally effective with the slurry of our calves,” the farmer concluded optimistically.
Otto Maier‘s farm
No floating layer, a better flow in the slurry channel
Otto Maier runs a dairy cow farm with a herd of 50 cows and their calves and manages 36 hectares of grassland (trefoil-grass and maize) in Seeon in Upper Bavaria.
With his vehicle fleet he also works as an agricultural contractor in his region around Lake Chiemsee. He was first introduced to Eminex® by his nephew Stephan at the start of 2021. The expectations for the use of Eminex® were clearly defined. “In some places I had to stir the slurry for an hour and a half to break through the thick floating layer. I hoped that Eminex® would help me to save time and make my slurry more fluid,” shared Otto Maier. And so it wasn’t long until he tried it out for the first time. “We used a telescopic handler to position the big-bag above the slurry pit. We then cut a 5 cm hole in the big bag with a telescopic knife and added the Eminex® to the flowing slurry just a few metres behind the agitator.” He summed up the results as follows: “Overall, the slurry was far more homogeneous than before and no longer formed a floating layer. I only had to stir it for 10 minutes and then spread the slurry with the injector.”
Automatic dosing
Since using it for the first time, Maier has now automated the Eminex® application on his farm. With the help of a dosing unit, every 20 minutes a few grams of Eminex® is added to the slurry directly in front of the dam. This means that the slurry is treated before it even enters the pit. “The dosing works perfectly without any effort needed on our part! The reservoir only needs to be refilled with Eminex® every few weeks, apart from that it runs itself,” he reported happily. “Before the slurry didn’t flow perfectly through the pipe into the pit and often accumulated at the dam. Thanks to Eminex®, I no longer have this problem.” As Eminex® is added to the slurry before the dam, no gas, which can go against the direction of flow and prevent drainage, builds up in the pipe. He added, “It’s a good knowing that with a simple step like this, I can make a small contribution to protecting the environment.”
Stefan Matter‘s farm
“I can save myself one or several work steps and help to protect the environment at the same time.”
At least that’s what Upper Bavarian farm Stefan Matter thinks. He runs a farm in Obing near Lake Chiemsee with his wife and children.
In addition to growing maize, grains and maintaining grassland on 56 hectares, the family also runs a farm shop and has 60 dairy cows plus their calves. “For me it is very important to have a cycle that is as closed as possible when it comes to biology and fixing ammoniacal nitrogen. As such, I produce the feed for our cows on the farm and fertilise with slurry,” explained the trained agricultural business expert. “When I heard about the new processing additive Eminex® and about how it improves the quality of your slurry and even reduces methane, CO2 and nitrous oxide emissions, I really wanted to try it.” The first application was done in the slurry pit in January 2022. “Before moving the slurry to its intermediate storage, I mixed in the recommended quantity of Eminex®. It was then moved and when it was time for spreading, I only needed to stir the slurry for a few minutes,” reported Matter. “The slurry now flows more evenly, is more homogeneous and, above all, helps me to save on mineral fertiliser”.
The Upper Bavarian farm also recently started using an automated dosing system. Before this was installed Matter explained that “the slurry would block up the connecting pipe every now and then.” “This problem was largely due to the solid material in the slurry. This couldn’t flow away because the methane bubbles that formed moved in the opposite direction to the slurry.” As the slurry is now treated before it reaches the dam thanks to the automated dosing system, methane can no longer form. “The slurry now flows smoothly through the connecting pipe and into the pit. I think that it’s fantastic that this product not only resolves the problem but also eliminates the cause and that it helps me to make a contribution to protecting the environment.” The farmer’s verdict is unequivocal: “I want to continue using Eminex®. I would particularly like to try and test this product with our younger cows as the slurry is often thicker due to the increased use of straw. I also hope to see a greater homogeneity in the slurry, a smoother flow during spreading and am looking forward to seeing its effects on my grassland.”
Application recommendation
• The application rate always refers to the amount of slurry in the pit at the time of application.
• Spread Eminex® slowly into the slurry pit while stirring it. Empty a big bag within 30 minutes. For slurry channels longer than 300m, it is recommended to dose Eminex® at two points.
• Always apply Eminex® behind the agitator to the slurry that is flowing away.
• Never add large quantities of Eminex® to slurry that is being stirred (risk of crust formation).
Winter storage
• Dosage of 1 kg Eminex® per m3 slurry every 12 weeks
Summer Storage
• Treatment of residual slurry with 1 kg Eminex® per m3 slurry after each slurry spreading.
• If no slurry is spread for more than 6 weeks, the slurry needs to be treated again with 1 kg Eminex® per m3 slurry.
• Adding 2kg of Eminex® per m3 of slurry while stirring it.
• Application usually takes place at the beginning of the winter season.
• A single application is usually sufficient to inhibit foaming during the entire winter storage period.